电池级硫酸钴蒸发结晶工艺设计及设备选型
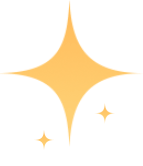
随着国内外新能源电动汽车动力电池的发展势头愈发强劲,镍钴锰酸锂正极材料因具有容量高、热稳定性能好、充放电电压范围宽等优良的电化学性能而备受追捧。镍钴锰酸锂正极材料中的钴元素可以提高正极材料的电子电导率,使离子混排现象得到有效抑制,进而稳定正极材料的层状结构,提升正极材料的倍率性能和循环稳定性。硫酸钴是生产镍钴锰酸锂正极材料的关键原材料,其蒸发结晶工序直接决定硫酸钴产品的质量。
本文基于国外某电池级硫酸钴蒸发结晶车间的设计,对硫酸钴蒸发浓缩、结晶、离心、干燥和筛分包装工序的若干工艺参数、相关设备选型等进行总结,以期为相关项目提供参考。
某厂以氢氧化镍钴的中间产品为原料,采用“常压浸出- 萃取- 蒸发结晶”的湿法工艺,年产约29 000 t电池级硫酸钴产品。硫酸钴蒸发结晶车间所使用的硫酸钴溶液的物性参数见表1。
经萃取净化的硫酸钴溶液送至车间后,首先进入蒸发系统进行蒸发浓缩。当溶液浓缩至理想浓度后,送至结晶装置中降温结晶,产出的晶浆经离心后,得到湿硫酸钴和硫酸钴母液。湿硫酸钴经干燥工序处理,去除表面水后,再经筛分工序得到符合外售要求粒径的硫酸钴晶体。筛分工序除筛出产品外,还产生不符合外售粒径的硫酸钴晶体——筛上大颗粒(图1中的大颗粒硫酸钴)和筛下小颗粒(即图1中的硫酸钴粉料)。大颗粒硫酸钴经破碎后与小颗粒硫酸钴被二次冷凝水重新溶解后送回蒸发浓缩工序。离心产生的硫酸钴母液一部分送至蒸发浓缩工序作为原料液,另一部分用二次蒸汽冷凝水稀释后送至溶剂萃取车间用于萃取有机相的转皂,转皂后液送至废水处理工序。工艺流程如图1所示。
2.1 蒸发浓缩
目前应用于硫酸钴蒸发浓缩的主流工艺有多效蒸发和MVR蒸发两种。多效蒸发的热源为生蒸汽,对于浓度低且处理量大的物料,其蒸汽消耗量非常大。尤其对于需要外购蒸汽的企业,多效蒸发的经济效益主要受蒸汽价格波动影响。随着目前市场蒸汽价格的上涨,产品成本中蒸汽成本的占比不容忽视。MVR蒸发的主要特点是将蒸发器蒸发料液产生的二次蒸汽,经压缩机压缩后,使其温度、压力升高,在整套MVR系统中循环利用,由此可以充分回收利用二次蒸汽的热能。在MVR蒸发系统中,蒸汽压缩机的蒸发系统的匹配程度以及抗波动性直接影响MVR蒸发的性能、稳定性和可靠性。与影响多效蒸发的主要经济性指标是生蒸汽消耗量不同,影响MVR的主要经济性指标为耗电量。
本工程由于建设单位在工程所在地附近建设有电厂,可提供充足的生蒸汽,而无需外购生蒸汽,故蒸发工序使用生蒸汽的相对成本比用电低。此外,本工程所在地为海外, MVR蒸发所配套的蒸汽压缩机的后期保养维修成本较高。因此,本项目采用多效蒸发工艺。
多效蒸发工序选用三效逆流蒸发工艺,通过高温蒸发脱除硫酸钴溶液中的部分水分,使得硫酸钴溶液浓度增大,进而达到结晶所需的过饱和度。工业蒸发过程一般需要考虑沸点升高、节约能源、物料的工艺特性以及从二次蒸汽中分离夹带的硫酸钴等问题[4]4]。蒸发工序的原料为经萃取净化后的硫酸钴溶液,根据该溶液的物化性质,设计时取沸点升高为3 ℃。为达到良好的结晶效果,蒸发浓缩后液的比重不应低于1.50。硫酸钴蒸发工序的主要工艺参数见表2。硫酸钴蒸发设备的运行消耗见表3。
蒸发工序消耗生蒸汽产生的冷凝水,经收集后送至萃取车间,用于调酸。为了减少蒸发产生的二次蒸汽夹带造成的硫酸钴损失,蒸发器设置了捕沫装置,二次蒸汽经末效冷凝器冷凝后产生的二次冷凝水中钴金属含量设计值不超过50 g/t。
蒸发浓缩工序设备的过流部件(如泵、蒸发器、管道等)材质选用钛材,非过流部件材料选用316L不锈钢(生蒸汽管道允许使用碳钢)。
2.2 结晶
工业上常用的硫酸钴结晶生产工艺分为间断结晶和连续式结晶[5]。间断式结晶的主要设备为结晶釜,结晶釜带有夹套和搅拌器。釜内为蒸发浓缩后的硫酸钴溶液,夹套通入循环冷却水。蒸发后液与循环冷却水进行热量交换,经过搅拌、降温、结晶、浓缩、再降温、结晶等步骤,产出含有满足粒径要求的硫酸钴晶体的晶浆。连续式结晶的主要设备为结晶器,蒸发浓缩后的硫酸钴溶液在结晶器内通过闪蒸降温冷却来实现结晶过程。目前应用于硫酸钴结晶的结晶器类型有DTB型结晶器和OSLO型结晶器。
间断式结晶工艺因单釜作业存在生产率和自动化程度低等缺点,且伴随着连续式结晶工艺的日趋成熟,除小规模生产外,间断式结晶工艺已逐渐被连续式结晶所取代。基于此,并考虑到该厂生产规模较大,结晶工艺选用连续式结晶。为选取合适的结晶器类型,对比了DTB改进型结晶器和OSLO结晶器,结果见表4。
从表4可知,与OSLO型结晶器相比,DTB型结晶器无需配备冷冻机组,能耗较低,且具有结晶器体积较小以及单体产能大等优势。基于以上分析,连续式结晶工艺选用DTB型结晶器。
考虑到选用单套设备会存在因不可预见的设备故障而导致整个车间停产的风险,结晶工序共选用两套硫酸钴结晶成套设备。来自蒸发浓缩系统的蒸发后液在结晶器内经闪发降温后析出硫酸钴晶体。硫酸钴浆液再用泵送至结晶缓存罐,由结晶缓存罐底部放料自流至离心机。与蒸发浓缩系统类似,为了减少料液在结晶工序闪发所产生的二次蒸汽夹带而造成的硫酸钴损失,结晶器同样设有捕沫装置,二次蒸汽经表面冷凝器冷凝后产生的二次冷凝水中钴金属含量不超过50 g/t。
硫酸钴结晶工序的主要工艺参数见表5。硫酸钴结晶工序的运行消耗见表6。
结晶工序的过流部件材质选用要考虑温度:当温度超过60 ℃时,选用钛材;当温度低于60 ℃时,选用316L不锈钢。
2.3 离心
结晶工序结晶缓存罐中的硫酸钴晶浆自流进入离心工序,进行过滤。离心工序的主要目的是:尽可能将结晶母液分离出去,得到湿硫酸钴晶体,同时应最大限度避免晶体在过滤过程中被破坏,保证晶体颗粒的完整性。
目前可实现硫酸钴连续生产的离心机主要有单级活塞推料过滤离心机、双级活塞推料过滤离心机和卧式螺旋卸料过滤离心机。从离心机的脱水效果来看,卧式螺旋卸料过滤离心机>双级活塞推料过滤离心机>单级活塞推料过滤离心机,即卧式螺旋卸料过滤离心机的脱水效果最好,单级活塞推料过滤离心机的脱水效果最差。从离心过程对晶体形貌的破碎程度来看,卧式螺旋卸料过滤离心机>双级活塞推料过滤离心机>单级活塞推料过滤离心机,即卧式螺旋卸料过滤离心机对晶体形貌的破化程度最大,单级活塞推料过滤离心机对晶体形貌的破化程度最小。
由于硫酸钴晶体粒径较小,市场对其形貌要求不高,基本无需考虑离心机对晶体形貌的二次破坏,而硫酸钴晶体的含水率对其市场价格影响更大;此外,综合考虑设备造价运行成本等因素,离心工序选用脱水效果更好的卧式螺旋卸料过滤离心机。
为匹配下游干燥工艺的单台流化床稳定运行的最大产能,共选用4台LLW530N型卧式螺旋卸料过滤离心机,分2组,每组1用1备配置。单台离心机的技术参数见表7。
离心机的过流部件材质选用316L不锈钢,非过流部件材料选用304不锈钢。
2.4 干燥
目前工业上主要应用流化床对湿硫酸钴进行干燥处理。流化床主要分为固定式流化床和振动流化床。相较于振动流化床,固定式流化床具有单台产能大的优点,但从目前的实际应用情况来看,其存在床板找平困难、床板易裂、易堵塞等缺点。为了规避单条生产线发生因设备故障而停产的风险,车间设计两条干燥产线,各使用一台流化床,单条产线的硫酸钴产能为15 000 t/a, 选用常规振动流化床即可满足产能要求。因此,干燥工序选用2台振动流化床。
值得引起注意的是,为干燥工序供料的上游离心机是连续作业设备,离心产品含水率受结晶工序颗粒粒度分布和晶浆浓度波动影响,因而进入干燥工序的湿硫酸钴水分必然存在波动。因此,为保证生产的稳定性,干燥工序的设备处理能力一定要考虑适当的富裕系数。此外,考虑到现场工作环境和环保等因素,干燥主体设备的配套收尘设施同样要考虑适当的富裕系数。结合工程经验,单台流化床的产能选为18 000 t/a。
湿硫酸钴在振动流化床中流态化并充分干燥。干燥按区域分为热风区及冷风区,确保产出干燥后的硫酸钴不会因为温度高于室温再次返潮。为了避免干燥风中的异物进入产品,降低产品质量,振动流化床进风口配置有空气过滤装置。干燥风通过鼓风机及冷却风机引入流化床,需要经过初效、中效、高效过滤。鼓风机输出的常温风经蒸汽加热器后进入流化床,在流化床的末端引入不加热的过滤空气。在流化床干燥硫酸钴的同时实现对异物细粉的初步分离,细粉随干燥的排气经收尘系统收尘,且充分洗涤后达标排放。为了保护环境和提供良好的现场劳动条件,振动流化床干燥成套设备附属的收尘系统采用一级旋风、两级水膜除尘工艺,收尘后外排空气粉尘含量不高于30 mg/m3。
此外,考虑到项目所在地空气湿度较大,为保证产品含水率小于0.2%,经过滤装置处理后的干燥用空气需采用转轮除湿机进行预处理,保证处理后的空气湿度<6 g(H2O)/kg。干燥工序的设计应尤其重视项目所在地的湿球温度。若湿球温度无法满足设计要求,干燥用空气在引入流化床前应先进行除湿。
单台振动流化床干燥设备的主要工艺参数见表8。
单台振动流化床干燥设备的运行消耗见表9。
干燥工序选用的振动流化床除支撑钢架使用304不锈钢外,其余材料均为316L不锈钢。
2.5 筛分与包装
干燥工序送出的硫酸钴晶体,依次经过Z型斗式提升机、除磁器、直线振动筛。直线筛分两层,上层筛网规格为8目,下层筛网规格为40目。8目筛筛上物引入破碎料仓,经破碎机破碎后进入暂存料仓;40目筛筛下物引入面料料仓后经过底部放料阀放料进入暂存料仓,由气力输送系统送至溶晶釜中,使用蒸发浓缩和结晶工序产生的二次冷凝水溶解后重新进入蒸发浓缩工序;8目筛筛下物和40目筛筛上物为合格产品,引入产品料仓,并送入包装工序。硫酸钴晶体的粒径分布如图2所示。
进入包装工序的硫酸钴经过吨袋包装机打包后,依次经过复检、扎口、贴标和覆膜缠绕后,使用叉车送入产品仓库中待售。
筛分包装工序共选用两套成套设备,各自独立工作,共享用一台覆膜包装机。硫酸钴筛分包装工序主要工艺参数见表10。
由于三元前驱体生产对硫酸钴中磁性异物含量的要求较为严苛[6],设计生产过程中应避免磁性异物的引入。为使产品质量满足国家相关标准,包装工序在Z型斗提机出料口设置永磁旋转型除铁器,在直线振动筛-8~+40目物料的出口安装自动清理永磁抽屉型除铁器,在产品料仓出料口安装手动清理永磁抽屉型除铁器。筛分与包装工序设备与物料接触部分材质选用316L不锈钢,其余材质选用304不锈钢。
本次电池级硫酸钴蒸发结晶车间的工艺设计和设备选型,从工程本身的实际情况出发,对其涵盖的蒸发、结晶、离心和干燥等环节的主流工艺和设备应用情况进行了分析和比较,选择“多效蒸发- 连续结晶- 卧式螺旋离心- 流化床干燥”的工艺。该工艺具有运行稳定、产品质量高、设备后期维修保养费用低等优点,可为类似工程的设计提供参考。转自有色冶金节能,作者:潘苑罡
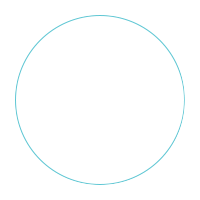